Report: An alternative to clear-felling radiata pine
By Mark Bloomberg, Eric Cairns, Denny Du, Harriet Palmer and Chris Perry, February 2019.
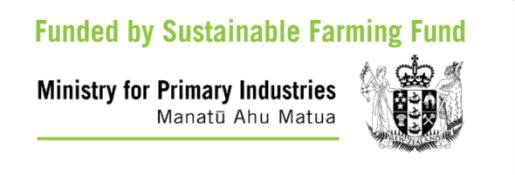
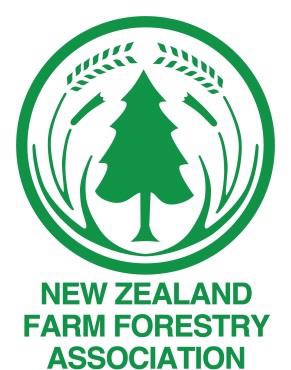
Background to the project
Members of the project team all have a long-held interest in continuous cover forestry systems. In 2018 we obtained funding from the MPI Sustainable Farming Fund to undertake a feasibility study: ‘Alternatives to clear-felling for radiata pine’. The following document provides a summary of the main outcomes of this project.
Target diameter harvesting
Target diameter harvesting (TDH) is selective felling and extraction of individual trees once they reach a certain diameter. A successful and well-known TDH system based on radiata pine is found at Dr John and Rosalie Wardle’s property, Woodside, Oxford, North Canterbury.
Natural regeneration of the crop species occurs within the gaps created as trees are harvested. This natural regeneration can be enriched by planting if the distribution or quantity of the new crop is inadequate. The naturally regenerated crop requires a different approach to management compared with a conventional single-age plantation crop, but the end product – high-quality logs – is the same as in any well-managed forest. As with other CCF systems, TDH leads to the conversion of an even-aged plantation to an uneven-aged forest; the forest can then be managed on a sustainable continuous cover basis, with regular selective harvesting, in perpetuity.
The question this project aimed to answer is: ‘Can the Woodside TDH system be profitably applied to other radiata pine woodlots?’
Our approach was to take four representative radiata pine woodlots of varying size, three in Greater Wellington and one in Hawke’s Bay, and assess the operational, marketing and economic feasibility of applying TDH to each woodlot.
In each case, pre-harvest forest inventory was undertaken, followed by modelling to grow the forests forward and simulate harvests (i) over twenty years using TDH and (ii) a comparative clear-fell operation at the optimum time. Growth and yield modelling was based on standard regional radiata pine growth models (YT Gen) combined with inventory data, enabling harvest volumes and breakdown of different log types to be forecast for each woodlot at any given harvest time. Standard discounted cashflow investment analysis techniques were used for financial analyses.
The model gave us the means to evaluate TDH at the four different case-study sites under a number of different conditions (e.g. different target diameter, frequency of harvest, discount rate). The metric used for comparing TDH vs clearfell harvesting is described as the Land Expectation Value (LEV)1.
Ultimately we were able to generate comparative financial outcomes over time for the two harvesting systems – TDH and clearfelling - in each case-study woodlot.
In addition, we assessed the practical feasibility of undertaking target diameter harvesting by visiting the case-study sites, and interviewing harvesting contractors and others in the log supply chain to seek their views on TDH.
Results of our analysis – some examples
The following graphs are examples of what the model developed during the project can produce.
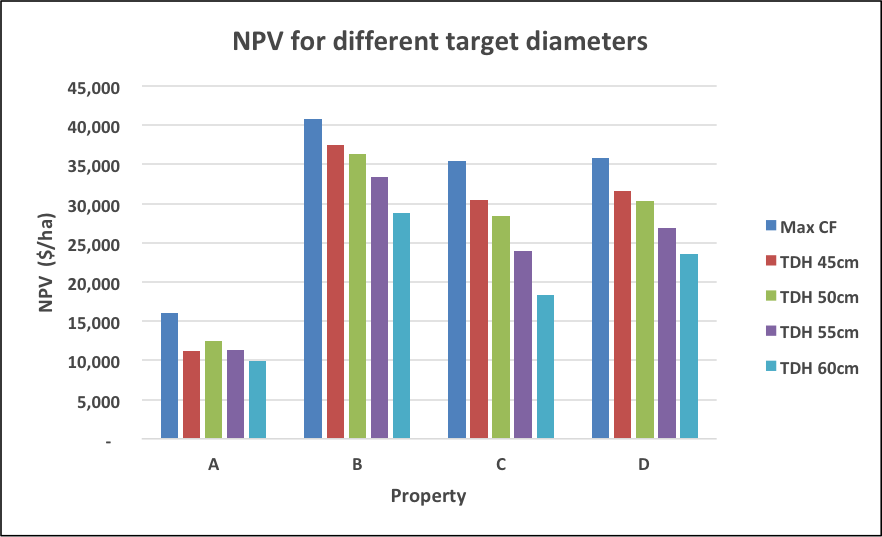
Model outputs for one of our case-study properties
The two graphs below show how the outcome of changing the frequency of harvest. Fig 2a shows the harvest on a tri-ennial (one year in three) basis, while Fig 2b shows the harvest if the forest was logged every year.
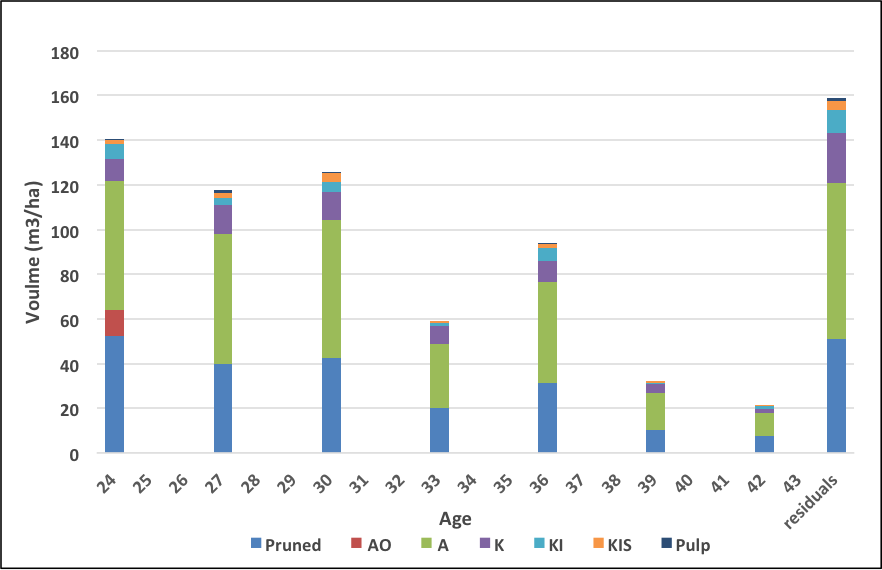
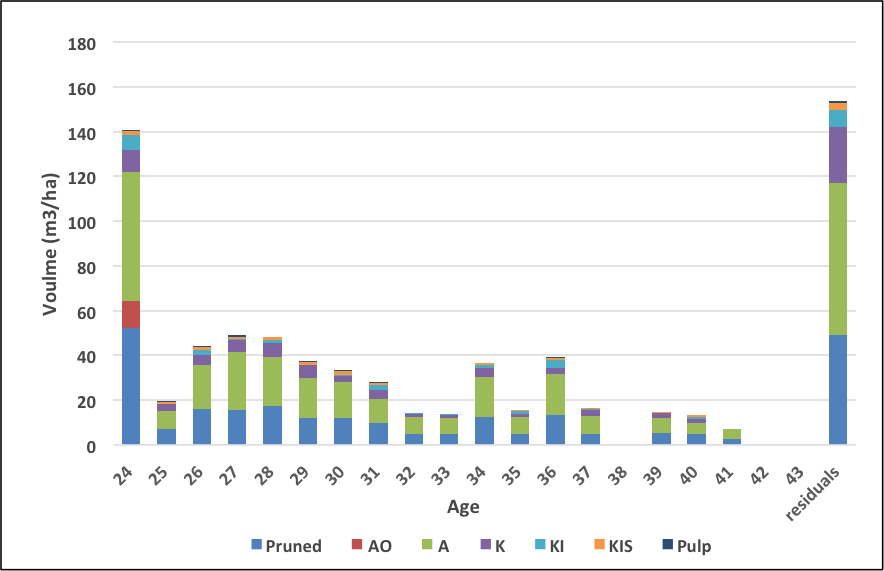
Where a forest which is approaching maturity is brought into a TDH regime, rather than harvesting all the trees which meet the minimum diameter at the first harvest, one option would be to set a limit on the volume extracted at any one harvest. This will reduce the impact of logging and begin the process of converting the forest to a true un-even aged profile. Fig 2c shows Property B under a 55cm tri-ennial TDH regime with a maximum harvest volume of the average volume of 83m3/ha per harvest. This volume equates to slightly higher than the mean annual volume increment predicted in YT Gen. It is conceivable that this harvest volume could continue long enough for the next generation of crop trees to be reaching maturity and that a steady harvest volume may be achievable in perpetuity.
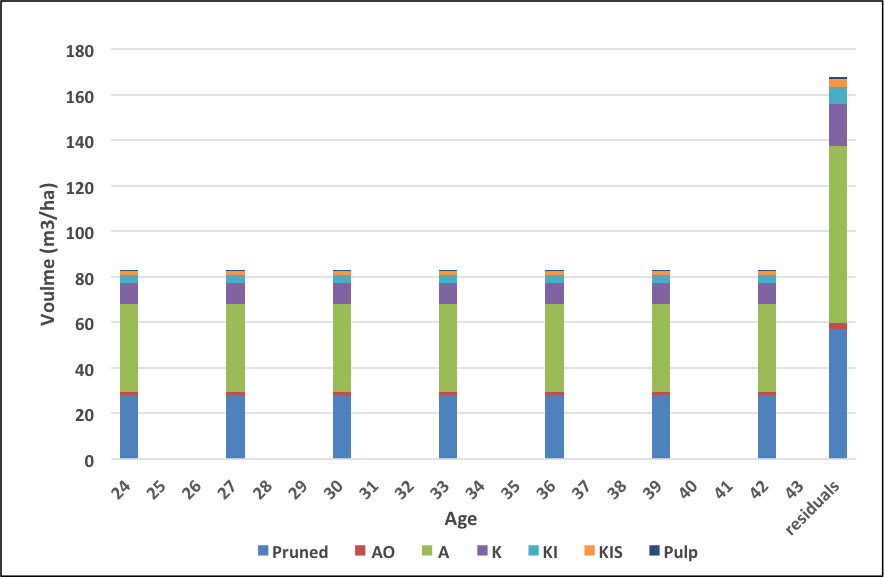
The economic feasibility of TDH: overall conclusions based on modelling outputs
In all four properties TDH was predicted to result in a profitable harvest albeit with a significantly lower NPV than the clearfell, with differences ranging from 35% - 55% of NPV under a clearfell regime. This result is consistent with other studies completed on TDH in New Zealand.
The difference in economic performance can be thought of as the economic cost of using a TDH system to sustain the ecosystem services provided by the forest and lost at harvest under a conventional clearfell regime.
Predicted harvest volumes varied significantly year-on-year for each forest. Better consistency was achieved with a tri-ennial harvest cycle as demonstrated for Property B. Harvesting more volume less frequently will also likely improve efficiency and reduce logging costs per tonne as fixed costs will be spread over greater volume.
The high percentage of ‘residual’ trees modelled not to achieve the 55cm target diameter over the 20-year harvest period highlights the shortcomings of using stand level modelling and raises several questions. For example, will unharvested stems show an increased growth rate following harvest of adjacent trees? And if so, will this be significant enough to impact on economic performance of the regime? Conversely, if TDH was continued beyond the 20 years modelled and the residual crop spread even further how would the NPV be impacted?
Making Target Diameter Harvesting work in practice
Discussions with contractors led us to conclude that, because of the relatively specialised skills and machinery needed to efficiently and productively harvest trees on a TDH basis, the ideal scenario would be for specialist TDH harvesting crews to become established in a given area. These crews could then develop a ‘working circle’ of properties managing their trees on a continuous cover basis.
What area of forest would be needed to keep a three-man crew working year round?
The following table uses harvest projections from our model for the four properties and as an example provides an indication of the approximate number of days work for a three-man crew, if each of the properties were part of an annual harvesting cycle.
Property | Area (ha) | 2018 | 2019 | 2020 | 2021 | 2022 | 2023 |
---|---|---|---|---|---|---|---|
A | 103 | 2,112 | 999 | 670 | 1,854 | 1,597 | 1,679 |
B | 39.2 | 2,352 | 2,352 | 2,352 | 2,352 | 2,352 | 1,490 |
C | 15.6 | 936 | 936 | 936 | 791 | 468 | 577 |
D | 2.5 | 153 | 99 | 40 | 23 | 96 | 53 |
Total area | 160.3 | ||||||
Total TDH harvest | 5,553 | 4,386 | 3,997 | 5,020 | 4,512 | 3,799 | |
Days work for 3-man crew (@ 90 tonnes/day) | 62 | 49 | 44 | 56 | 50 | 42 |
In practice it is unlikely that all forests in a ‘working circle’ would be harvested every year. Our model allows for the selection of either one or three-year harvesting cycles, but the cycle could equally be two years or four years (although a cycle longer than three years may result in harvest volumes and the proportion of canopy removed becoming somewhat high).
Table 1 shows that around 160 hectares of mature/semi-mature forest in the lower North Island could provide an average of around 50 days of harvesting work a year for a three-man crew. Therefore, for a full year’s work schedule of around 200 days, a minimum of (4 x 160) = 640 hectares of forest would be required, but probably more, given constraints such as summer-only harvesting on some sites. Within a working circle of multiple properties of different sizes, there would likely be some suited to annual or biennial harvest, and others suited to a longer harvest interval.
Is there a minimum woodlot size below which TDH will not be economic?
There will be a minimum woodlot size below which TDH in radiata pine does not make economic sense, which indicatively we estimate to be around 10 hectares. This is because, even with a tri-ennial harvest (once every three years), the total harvest volume would likely be too small to attract a harvesting crew.
On the other hand, if the forest owner has the skills and machinery to be able to harvest a small number of trees and mill on-site with a mobile mill for on-farm needs, then TDH could work well in small woodlots. This approach has been proven with higher-value species. Milled radiata timber would still have to be taken off-site for preservative treatment.
Roading requirements
Earlier work by members of the project team has shown that overall economic performance of TDH is only weakly sensitive to changes in roading costs, and far more likely to be affected by log prices, log yield, and discount rate.
The question arises: would a forest owner need to build roads to the same standard for a TDH harvest, as for a clearfell harvest, or could somewhat lower specifications suffice, given the fact that lower volumes of timber will be transported at any one harvest? There would be a number of ‘it depends’ factors coming into play – for example site topography, geology/soil type, and TDH harvest volumes. There may also be various combinations of machinery that could significantly alter roading costs – for example, the use of forwarders to bring logs out of the forest to a landing close to the highway, adding costs to the extraction part of the process but reducing the need for new road building within the forest.
In our model, we used industry standards for the costs of roading, adapted according to our knowledge of the sites. This generic approach is adequate for modelling, especially given what we know about the sensitivity of roading costs to the overall economic outcome. In practice, and like any type of harvesting operation, the skill of the forest manager will be all-important in planning and costing TDH harvest infrastructure and logistics on each individual site.
Harvesting skills and machines needed
A critical practical element in determining whether TDH can be undertaken will be the availability of skilled harvesting contractors who are prepared to try something different to their normal clear-felling operations. In addition, new management skills will be needed to prepare forests for TDH, and manage the residual and regenerating multi-aged trees in between harvests.
The experience of Tony Brand of Brand Logging, Rangioira, who carried out a recent TDH operation at Woodside, was that using a feller-buncher (a machine which fells, de-limbs and moves stems) was less effective than using a motor-manual system – that is, a man with a chainsaw to fell the trees, and then a machine to winch the fallen trees out to the skid site, where they were processed and cut to length by machine. Reasons included difficulty in felling trees accurately with the feller-buncher, and problems with moving the machine efficiently within the forest. The Woodside target diameter is 60 cm dbh, so trees are relatively large at harvest, and this exacerbated the problems.
The harvesting industry is moving inexorably towards mechanisation for a number of reasons, including increased productivity (in clearfell harvesting operations) and safety. There is general consensus that, while there are skilled chainsaw operators working in the harvesting sector, these people are (a) in high demand (b) becoming increasingly expensive to hire and (c) will become harder to find as time goes on.
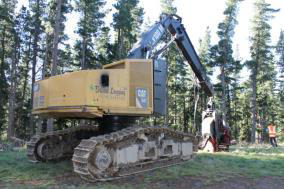
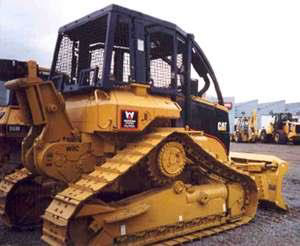
http://www.alliedsystems.com/
Whatever harvesting system is used, the work will require operators to develop new skills and operating systems. It will also require machinery at the smaller end of the spectrum. A recommendation from Tony Brand was a Caterpillar 517/527 tracked skidder, fitted with a winch and carrying light rope to allow longer lengths of rope (up to 100 m) to be pulled, thus reducing the need to position the skidder close to felled trees.
Development of more versatile machinery could help mechanised systems become better suited to TDH. For example, an excavator with an automatic coupler that can quickly swap between a feller/processor head, a grapple, and a bucket has been developed as part of the Forest Growers Research Steepland Harvesting programme. Such a machine could fell, shovel, extract, process and load logs as well and construct tracks and small processing sites. A machine that can carry out multiple functions will increase utilisation of machinery and potentially lower overall system costs.
Logging trucks suitable for TDH
An additional element to consider is the availability of logging trucks with the best specifications for the harvest in question. Logging trucks are generally 7, 8 or 9-axle, (7-axle is a truck and trailer) and, as with harvesting machines, there is a move by hauliers towards operating fewer, larger trucks. In general, 7-axle (28 ton payload) trucks are preferable for small-scale harvesting. The log haulier we spoke to said he would always keep some smaller trucks for woodlot harvests.
Self-loading trucks could work well with TDH operations where the harvesting contractor would likely only want to bring a minimum configuration of machines and crew on-site, and this configuration might not include a loader of any sort. Self-loading trucks are relatively rare, carry a smaller payload than other trucks, and add to the haulage costs for the forest owner because of the reduced payload and the time taken for the truck driver to load them.
Harvesting rates for TDH compared with clearfell
In our model and based on discussions with contractors, we used a generic TDH harvesting cost of $42/tonne; for the clearfell comparison, we used $35/tonne. In addition, we included a charge for self-loading trucks (additional $2/tonne), and a $3/tonne differential for management costs to cover the extra cost of marking individual trees in TDH.
All these costs will vary according to the individual circumstances of each harvest, and the model can be adjusted as required. However, we conclude that generally TDH harvesting will cost significantly more than clearfelling, perhaps by as much as $10-$20/m3.
Carbon implications of TDH
Our economic model does not include income from carbon in any scenario, clearfell or TDH, and we were unable to draw any firm conclusions about whether a TDH system will offer owners any net financial advantage in terms of extra carbon credits compared to a clearfell system. Continuous cover forests managed for production are ‘permanent’, but do not fit the ETS criteria for permanent forests because of their regular harvests. The main challenge for ETS administrators would be to develop a measurement system which could cope with multiple age classes of trees and regular harvests, but without becoming too onerous and expensive.
Tentatively (and rationally), we suggest that there will be little difference in the average carbon balance in commercially managed continuous cover forests and clearfell systems over the long term.
Conclusions from the TDH feasibility study
Overall, the conclusions drawn from the study are:
- TDH is feasible, profitable, and could be made to work, especially if specialist harvesting crews were to become established in areas with a sustainable TDH harvest
- TDH of an initially even-aged forest is less profitable than clearfell harvesting if compared using standard investment analysis techniques under all scenarios in our case-study woodlots
- we are unable to draw any conclusions on the relative profitability of TDH in a ‘normal’ radiata pine forest (i.e. one with equal numbers of trees of all different ages) as this information is not available in New Zealand
- TDH could begin sooner than conventional harvesting, if export markets exist for low-density logs
- small woodlots (e.g. below 10 hectares) are unlikely to produce enough volume at harvest to make TDH viable unless the owner harvests the trees themselves
- in the current harvesting environment, the challenge for forest owners/managers will be to find harvesting crews prepared to do something other than clear-felling at a reasonable rate
- there are many non-financial benefits of TDH which cannot easily be valued but may be significant on some sites and to some owners. Whether owners believe these values are equal to, or greater than, the difference in financial returns remains to be seen
- TDH may have most potential on sites with high erosion risk, using mechanised harvesting systems that have yet to be developed
- a key unknown highlighted in this study is how sub-dominant radiata pine trees will respond in terms of growth rate once neighbouring dominant trees are removed
- we were unable to draw any firm conclusions about whether a TDH system will offer owners any net financial advantage in terms of extra carbon credits compared to a clearfell system.
Acknowledgements
This document was originally a handout for a field day at Tinui Forest Park near Masterton, February 20th 2019. Tinui Forest Park was one of the project’s case-study properties.
The project team would like to thank to following people for their support and contributions to this project:
- John and Rosalie Wardle
- Dave Gratton
- Chris Livesey
- John Upton
- Tony Brand
- Peter Davies-Colley
- Guy Farman
- Elizabeth Heeg
- Alastair Luke
- Steve McDougall
- Stuart Oliver
- Tim Thorpe
- Peter van Gosliga
- Tinui Forest Park
- PF Olsen consultancy team
- Woodnet inventory crew
We also thank the following for funding this project:
- MPI Sustainable Farming Fund
- Wairarapa and Wellington Branches of the NZFFA
- Tinui Forest Park Ltd.
The Project Team
- Mark Bloomberg, University of Canterbury School of Forestry
- Eric Cairns, Wellington Branch, NZFFA
- Denny Du, PF Olsen Consultancy Team
- Harriet Palmer, Tinui Forest Park/Wairarapa FFA
- Chris Perry, PF Olsen, Napier
Project outputs available/coming soon
- Demonstration version of the TDH model
- Video of harvesting at Woodside
- Tree Grower articles, Feb 2019 and May 2019
- NZ Journal of Forestry article
Woodside – Target Diameter Harvesting in practice
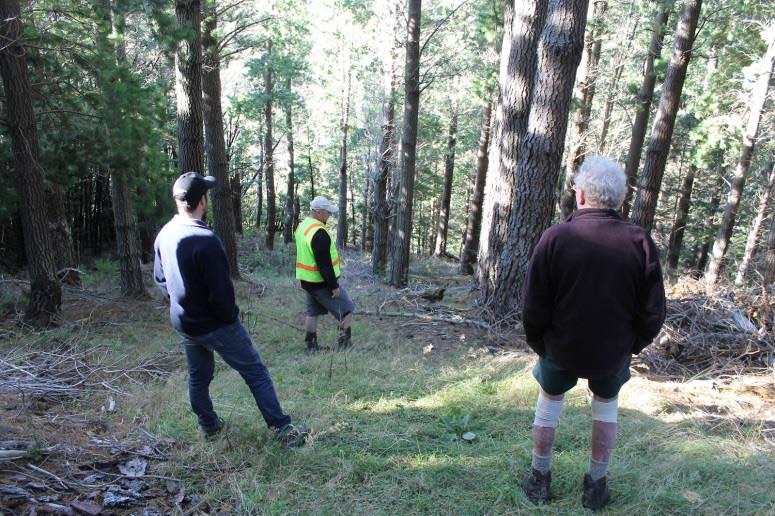
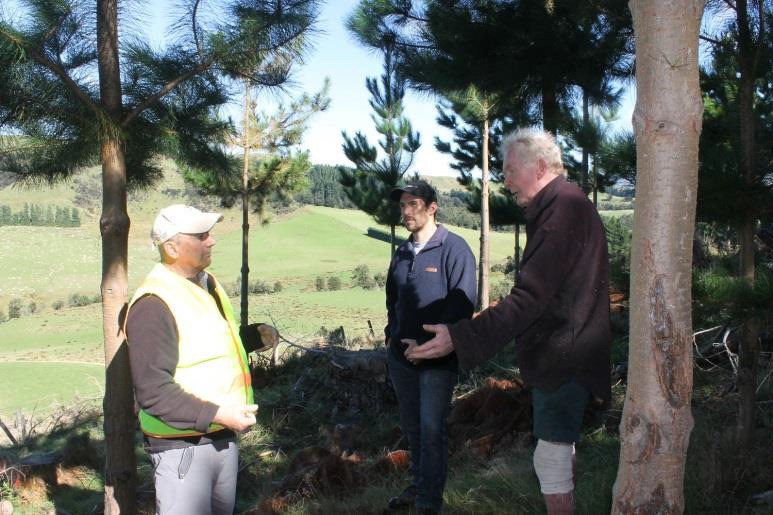
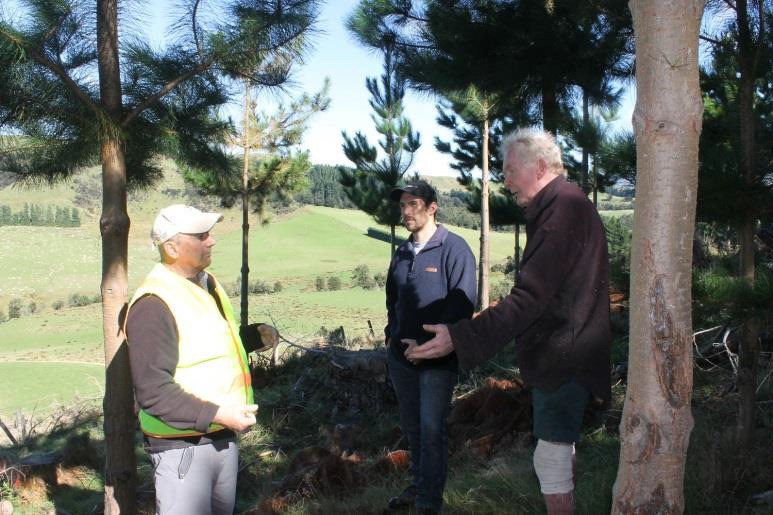
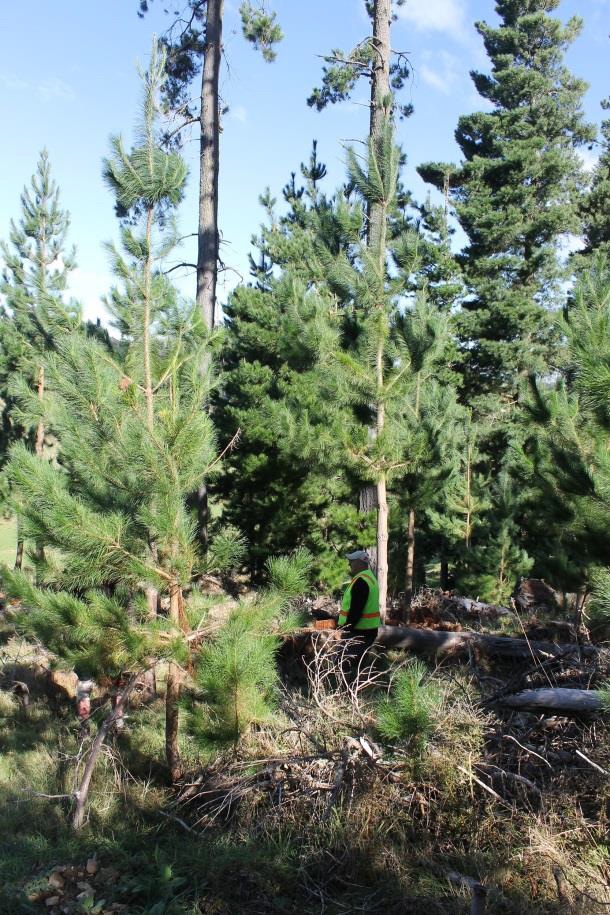