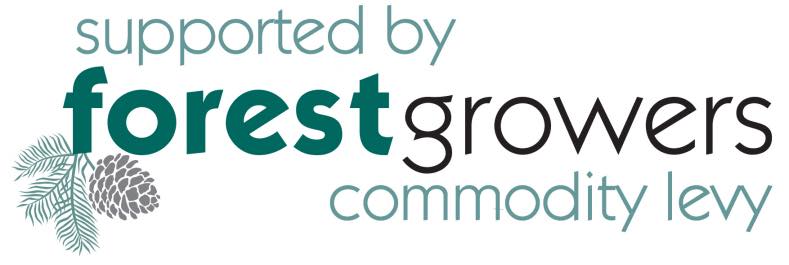
This is free.
Harvesting Innovation Workshops
By G. West and J. Schrider, December 2019.
In this page:
Summary
From six workshops on harvesting innovation of small-scale forests, we have gained some very useful insights into recent developments. We have also updated a key group of levy stakeholders on research outcomes and current trends.
The previous “Steepland Harvesting” PGP programme has resulted in the development of significant forest harvest engineering infrastructure, especially in winch assisted felling. Due to a recent emphasis on Health & Safety and greater harvesting mechanisation, lower accident rates have also been achieved in these operations. However, greater mechanisation has increased capital costs and an associated rise in harvesting costs. On steep terrain where winch assisted ground-based felling has been adopted, fewer mid-slope tracks are required and hence have reduced environmental impacts.
Winch assisted traction machines previously developed in New Zealand are now available more cheaply from overseas and this may be a continuing trend.
Harvesting costs of small-scale forest growers appear to be reduced by a change to lower cost forwarders through innovations with 4x4 agricultural trucks and 8x8 tractor/trailer units. These require lower quality roads for two-staging using sort-and-load yards near roads. These systems are still coupled with large (full scale) harvesters and loaders, because smaller-scale farm forestry trees are no smaller or easier to harvest than trees in larger scale operations. The general trend is toward fewer machines where possible, fewer workers, lower capital costs, and multiple use of machines.
These workshops have resulted in three tasks being identified for further work. Proposals have been developed and discussed by the SME Committee. These have been supported by the SMEC and recommended for funding by the FGLT.
A need emerging from these workshops was for information systems and processes to help raise the level of knowledge of small-scale growers about harvesting and marketing. At all workshops we were asked about the provision of extension services, seminars, tools, and collaboration. This element will probably need to form a separate funding application, possibly to Te Uru Rakau.
Introduction
A series of workshops have been completed with funding from FGLT to establish the issues and innovations arising from the small-scale forest grower supply chain. We have been significantly aided by the Regional Wood Councils, NZFFA and FICA. We also spent considerable time engaging some key individuals that have a record of innovation and have tried to reach a broad constituency of stakeholders and interested parties.
These workshops were run during a period of rapid log price reductions and consequently many contractors were somewhat preoccupied with finding work and keeping their business’s viable. Many farm foresters were keen to learn what was happening in this area and some had woodlots due for harvest and wanted to become more knowledgeable of the business aspects.
Activities
To gather background research information, we collated existing reports and related articles in a shared “Drop Box” file with folders for information, contacts, pictures, and workshop outputs. This was shared with Venise Comfort, NZFOA.
To initiate the workshops, we prepared an introductory presentation of the current harvesting environment for small scale forest owners and explained how the current research funding process operates. Next, Keith Raymond (FGR) presented an overview of the recent Forest Engineering research developments and what is proposed in the new Harvesting & Logistics programme. To save costs, these slides were later presented by John Schrider at the last three workshops. These slide shows are available from the NZFFA web site.
Six (one more than planned) workshops were organised and held in Feilding, Gisborne, Rotorua, Blenheim, Whangarei and Balclutha.
In total the workshops were attended by about 111 people from many diverse organisations. For example, there were farm foresters, harvesting consultants, logging contractors, equipment sales representatives, regional council representatives and researchers. See Appendix 1 for list of attendees and Appendix 2 for Summary by category
Outputs
To summarise the output and collate the many ideas put forward, we have allocated ideas into themes and made note of existing and past research programmes to find categories that align.
Seven key themes emerged. These are:
- How to foster collaboration among small-scale growers at harvest time to reduce harvest costs and encourage equipment into the area. Also, how to market wood to smooth the flow to encourage logging/roading/transport contractors to develop a longer term commitment.
- Harvest planning tools to assist small scale growers to gain greater awareness of the issues faced by the logging contractor and to make better decisions at the time of planting to avoid a poor outcome in 25 years’ time. It was proposed that the existing tools PLANEX and CHPS could be amalgamated. However, they may possibly be too complex, so it was suggested a simpler decision support tool is required.
- How to achieve lower capital machinery costs with fewer machines and multipurpose machines combined with fewer crew if possible. While there have been major advances made in this area it seems a fruitful theme to pursue for small growers, particularly the shift to agricultural machines.
- Reduced roading costs. Substantial roading infrastructure is not valued by small scale growers. Farmers have a very different view on the quality of access needed when compared to corporate foresters. As road metal is a major proportion of costs, novel road surface material made from the forest is suggested, e.g. wood chunks, log corduroys
- How to better sell and market small-scale forests. The whole process of converting woodlots into cash appears (particularly to farmers) as unsatisfactory. This starts with methods of marketing (tendering, managed sale (with several variations), chain of custody, wood measurement, markets and transparency. Small-scale growers usually only experience forest harvesting once in a lifetime. For this to be a good experience to replant or encourage others, a better level of awareness and tools to help make decisions are required. This includes information and extension on log supply chains and better business management. Case studies on different methods offer one way of quantifying differences.
- Better use of residues as they accumulate on skids or stand edges. How to add value rather than cost in their utilisation. How to reduce the mess as perceived by farmers and reduce “bird’s nests” associated with hauler operations
- Mechanisation of waste and production thinning is occurring, and this may be a useful adjunct to this programme as many of the principles are in common. Mechanisation of pruning is associated with this and is important to small-scale growers.
A first rationalisation of these seven themes has suggested some will fit within the SME Committee’s mandate, others fit into existing research programmes. Some will fit with FGLT funding criteria for funding, and others may best suit the 1BT Fund in Te Uru Rakau.
|
Theme |
Proposal |
Funding source |
---|---|---|---|
1. |
Collaboration |
Next stage to the current SMEC “Aggregation of Small Forests” project. Examine and quantify benefits of methods of marketing woodlots. |
FGLT via SMEC |
2. |
Planning tools |
Next stage to “Woodlot costing tool”, access multiple geospatial layers to assist decision making. |
FGLT via SMEC |
3. |
Lower costs logging |
New Proposal to SMEC. Undertake a production study and define limitations of innovative small-scale harvest systems. |
FGLT via SMEC |
4. |
Lower cost roading |
Add to new Harvesting & Logistics Programme |
PGP |
5. |
A better wood selling experience |
Proposal to 1BT. Prepare information and extension programme. Document case studies, focus on business management. |
Via TUR |
6. |
Use of residues |
Add to new Harvesting & Logistics Programme |
PGP |
7. |
Mechanisation of silvicultural operations |
Check if in FGR new bid. Needs further development. |
SFFF |
Because the last workshop was in November at Balclutha, we had to provide an earlier draft, which we submitted as a FGLT proposal by 30th Sept via Venise Comfort for SME Committee to consider.
Items 1, 2 & 3 seem suitable for the SME Committee approval and FGLT consideration. These possibly can be packaged as one proposal.
Items 4, 6, & 7 could be managed into the existing PGP with Keith Raymond’s and FGR’s help.
Item 6 is predominantly extension and better suited to 1BT fund. While this is not research, FGLT does fund operations projects and we may need some FGLT or NZFFA co-funding to succeed with Te Uru Rakau.
On 3rd October a funding application for 3 items was presented to the SME Committee and was supported to proceed to the NZ FOA Secretariat for review. The summary of the proposal was:
Small scale forest grower harvesting innovation |
|
---|---|
This project involves three tasks that will benefit Small Scale Forest Grower (SSFG) levy payers. 1. Harvest planning. Investigate and develop a simple to use spatial tool that allows mature woodlot owners and small-scale forest investors to develop a rudimentary harvest plan. This continues with the work by Murphy & Visser (Woodlot analysis Tools, FGR, 2019, see “Additional information section” for link) that focuses on net return calculations. This project would leverage that work but will focus more on delivery of multiple layers of geospatial information via the internet. This is intended to: 1. inform small and medium forest growers of the forest engineering issues raised by geographical and regulatory information at harvest time and 2. avoid locating woodlots where returns are not going to satisfy investors. 2. Marketing and selling logs. Investigate methods of SMEs marketing woodlots when harvesting and quantify the differences between methods. Continue with the pilot aggregation study started in the Greater Wellington Region (Levack, Wallace, & Moore, 2019) that models continuous harvest scheduling and extend the pilot to examine methods of marketing and selling in two regions. 3.Innovative harvest systems. The Harvesting Innovation series of workshops run in 2019 identified several relatively unheard-of innovative systems for harvesting small forests. The project establishes production capacity of these systems (hence cost) in small forest locations and establishes production and cost templates for use by planning and harvesting managers as well as the owners of woodlots. |
Task three has involved the identification of innovative equipment or technologies for which no production or cost information has been previously described and publicised. For example, the broad harvest cycles i.e. road construction, felling, extraction, processing, handling, load-out and transportation in a small-scale forest setting. Basic system set-up will be described, work methods recorded, and work studies undertaken to measure production capability and performance. Cost templates will be designed from standard and known industry methodology with the end result a calculation of a logging cost.
The systems identified from workshops to date are:
-
Seaview Logging’s (8x8) Valtra Tractor and Trailer Forwarder
-
Seaview Logging’s (8x8) Valtra Tractor mounted mini winch & spar
-
Davies-Colley’s 4x4 “Baby Truck” Forwarder
-
T- Winch – Traction assist machine – Felling
-
T- Winch – Traction assist machine – Extraction
-
Continuous Cover Harvesting systems
Individual studies will then be extrapolated/interpolated to ultimately design 2-3 optimal harvest systems suited to small grower needs. Individual study results and optimal system solutions will be promoted via written reports and presentations at conferences and workshops. The overriding objective is to get small growers and system/machine innovators engaged and motivated to continue with future development.
Depending on the outcome of the request for further funding of the three proposals above, we have considered initiating a working group to guide the further development from this project and have a shortlist of candidates from the workshop attendees.
Conclusions
This FGLT project has proved to very worthwhile, mainly because of the level of engagement achieved and the clear need established to find ways of reducing harvesting and marketing costs for small scale forest owners. Many participants were seeking knowledge and took some time to get confidence to contribute and ask questions. Several equipment innovations were brought forwards and while some need further development, a formal level of quantifying the benefits of such equipment or system change is needed to understand where to proceed to next.
A clear trend of 100% mechanisation for health and safety reasons has been established in the large-scale forests, but this appears to be slower in adoption for those less established operators, who often start out in small scale forests.
Most data collected on safety and costs is exclusively supplied by large scale operations.
There seems to be a lack of communication and collaboration by key stakeholders in small scale forests. Growers, harvesting consultants, and logging contractors do not generally have a forum for communication. They do not engage well in levy research projects or tech transfer conferences. Possibly this is a task for a separate working group.
Workshop attendees by category
Presentations
Innovation in small scale harvesting (pdf)
Forest Engineering R&D in New Zealand - Workshop for Growers of Small forests (pdf)
