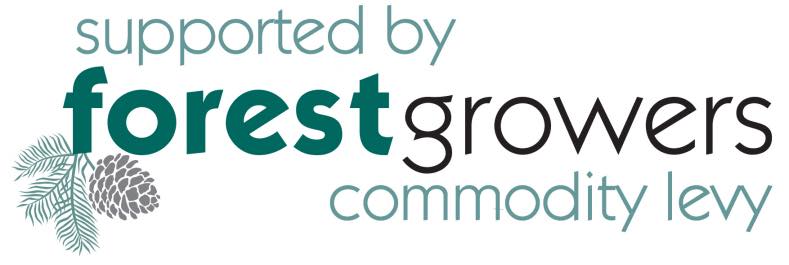
This is free.
Evolution or revolution in harvesting?
Keith Raymond, New Zealand Tree Grower November 2017.
As many small-scale growers prepare to plan to harvest their forests and woodlots planted in the 1990s, there is a quiet revolution being planned in how harvesting these forests on steep slopes can be carried out. Changes to harvesting crews to make them smaller with less machinery, to shrink the size of yarder landings and move log sorting off the landing are some proposed innovations.
The current move into harvesting mechanisation may have put more people into the safety of cabs, but it has done little to improve the overall economics of bringing logs off the hills. If anything, it has become more costly, especially in smaller forests and woodlots, threatening their viability.
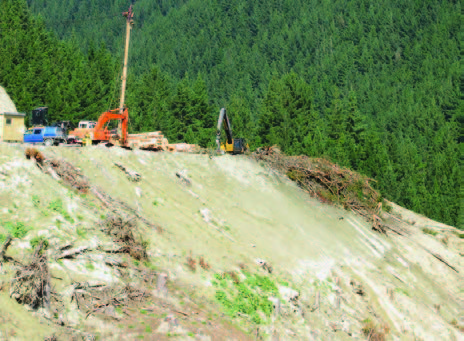
The other problem is that labour productivity has actually been falling and not increasing because hauler crews have more workers and lower production than ground-based crews.As we move forward and harvest the wood planted back in the 1990s, we need more hauler crews and know there is already a shortage of labour.The increased harvest will require around 100 extra contracting crews and 800 additional workers using current methods.
Research by Scion shows that the rising costs mean about 10 per cent of the small forest resource − up to 1.65 million cubic metres of wood a year − may be uneconomic to harvest. As harvesting increasingly moves into these forests on steeper land and in smaller, more isolated holdings, the challenges of maintaining international cost competitiveness and safe operations will increase. Added to that, pressure is coming on foresters in some areas to reduce the negative effect their operations are having on the environment.
These concerns have led to a re-think about how steep forests should be logged. Forest Growers Research – formerly known as Future Forests Research Ltd – has been leading the Steepland Harvesting programme.
Changing the process
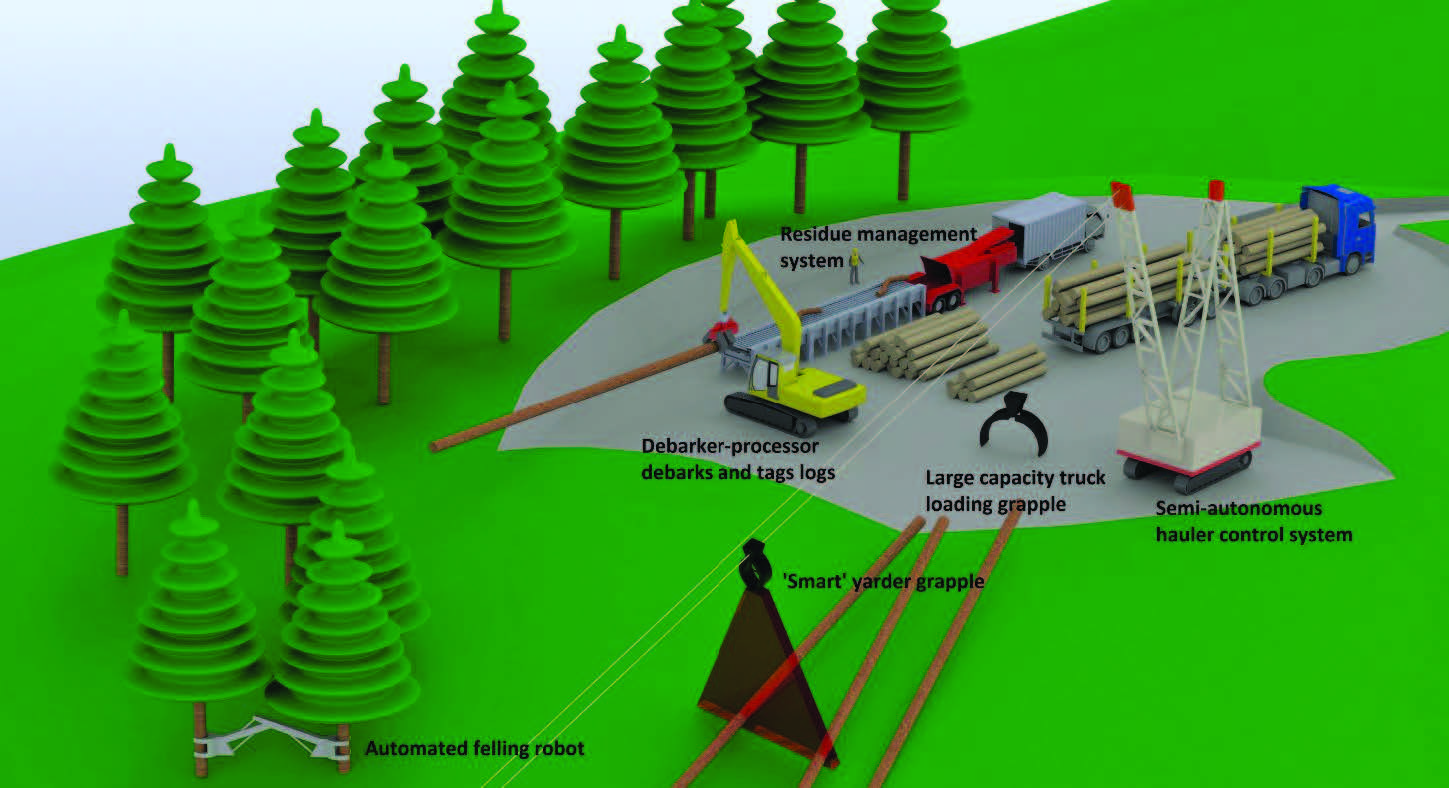
Forest Growers Research believes the time has come to re-examine the way they operate and come up with a complete redesign of the harvesting and log manufacturing process. The problems facing forestry are not going away and will only become more acute as the wood available for harvesting over the next decade rises to an expected 35 million cubic metres a year from the current level of around 30 million cubic metres.
Most of this increased availability is in small forests in remote areas where harvesting, processing and logistics costs will be higher than current costs.These costs have been rising considerably over the last five years and will probably continue to rise without much ability of the industry to control them unless something really different is done. We also need our labour productivity rates to be going up, not down.
Over the past seven years, harvesting research carried out by Forest Growers Research has concentrated on supporting developments in tree felling and log extraction such as the ClimbMax steep slope harvester, the Alpine grapple carriage, the CutoverCam, HarvestNav machine navigation technology and tele-operated felling and tail-hold machines.
New research programme
A proposed a new research programme now takes innovation to a new level and covers the whole of the forestry value chain. This proposal is designed to cover everything from harvest planning through to log delivery to the local mill or port.
Some of the ideas contained in the plan could appear to be quite radical compared with current logging practices. The proposal is for a new, automated harvesting and logistics system that will eliminate manual hazardous tasks, such as log branding, log measurement, quality control, stocktaking and truck load securing. It will automate functions to make tasks such as log extraction, processing and sorting easier, safer, less repetitive and more efficient. It foresees greater use of tele-operation with other tasks beyond tree felling, such as log hauling, log sorting and truck loading.
The new research programme has identified four main requirements which will help to solve the problems identified −
- Improve the economic harvesting of all forests by reducing costs and increasing labour productivity
- Design new jobs which draw from a wider pool of skilled employees who are attracted to the industry
- Further improve worker safety
- Reduce negative environmental effects and compliance costs.
The proposed multi-million dollar programme is planned to run over the next seven years and be jointly funded from the forest growers’ levy on log production and from the government through the Ministry for Primary Industries’ Primary Growth Partnership programme.An application for funding has already been approved to go to the next stage of the funding process. Work is focussed on completing a successful business plan to get the $5 million of government funding requested, in addition to $9 million in industry funding from the forest growers’ levy.
Reducing log handling
It is a big programme, probably about twice the size of the Steepland Harvesting programme, which has now been completed. Without the 40 per cent of government funding which adds to the contribution from the Forest Growers Levy Trust and the in-kind contributions from manufacturing partners, it would obviously have a major effect on what can be achieved. If the business case is turned down it will not halt the programme, but it will compromise its size and effectiveness, and would mean that the research may have to be spread over a longer period of time and some activities would have to be dropped.
What are the changes that this redesign of the steep forest harvesting and log manufacturing process will bring about? Constructed landing areas will shrink dramatically, with fewer machines working on them and there will be minimal log storage on the landing. One of the main objectives is to cut the number of times a log is handled before it reaches the mill or port, which will help to reduce costs.
Export logs are currently handled anywhere between eight and 12 times before they go on the boat. The aim is to reduce this multiple handling, especially on the landing, and do it more productively somewhere else. Overall, we could cut the number of times a log is handled by 50 per cent.
More log grades
However, the plan does not involve reducing the number of log grades which have to be cut in the forest to meet customers’ demands. If anything, the proposed new system will allow additional grades to be cut so that extra value can be extracted from each log.
Landing size is what limits the number of cuts. There has been a lot of research carried out over how many cuts a Waratah processor can handle. If you have to produce more log grades you have to build a bigger landing. This increases the cost because you often have to excavate into the hill and move more dirt to build a big landing in steep country.
Reducing log grades is not the answer to the landing space problem.The solution is to take the wood away from the landing to cut more grades, if that is what the market wants. Harvested logs will be transported away to separate automated log sorting and storage facilities.
Essentially, the proposal is for an advanced two- staging system. Under the plan, a landing would be reduced to a minimum size so there will be just enough room for the yarder and one processor-loader machine using a Quick Coupler to switch between log grapple and processor head.The processor would be positioned under the hauler boom to grab, process and stack to one side.Whole stem debarking would also be carried out before log making, to reduce the amount of chemical fumigation of export logs at the ports. The unsorted wood is loaded on to off-road trucks and taken to a separate sort yard, either along the roadside or any available space near the forest gate.
At the sort yard, a new robotic log sorting facility will scan and sort mixed grade logs as they arrive from the landing. A shape recognition scanner then calculates true volume eliminating manual log measurement and performs log quality control. Sorted logs will be put on to an automated loading gantry which will load the log trucks and secure the load using an automatic tensioning system with no chaining-up required by the truck driver.
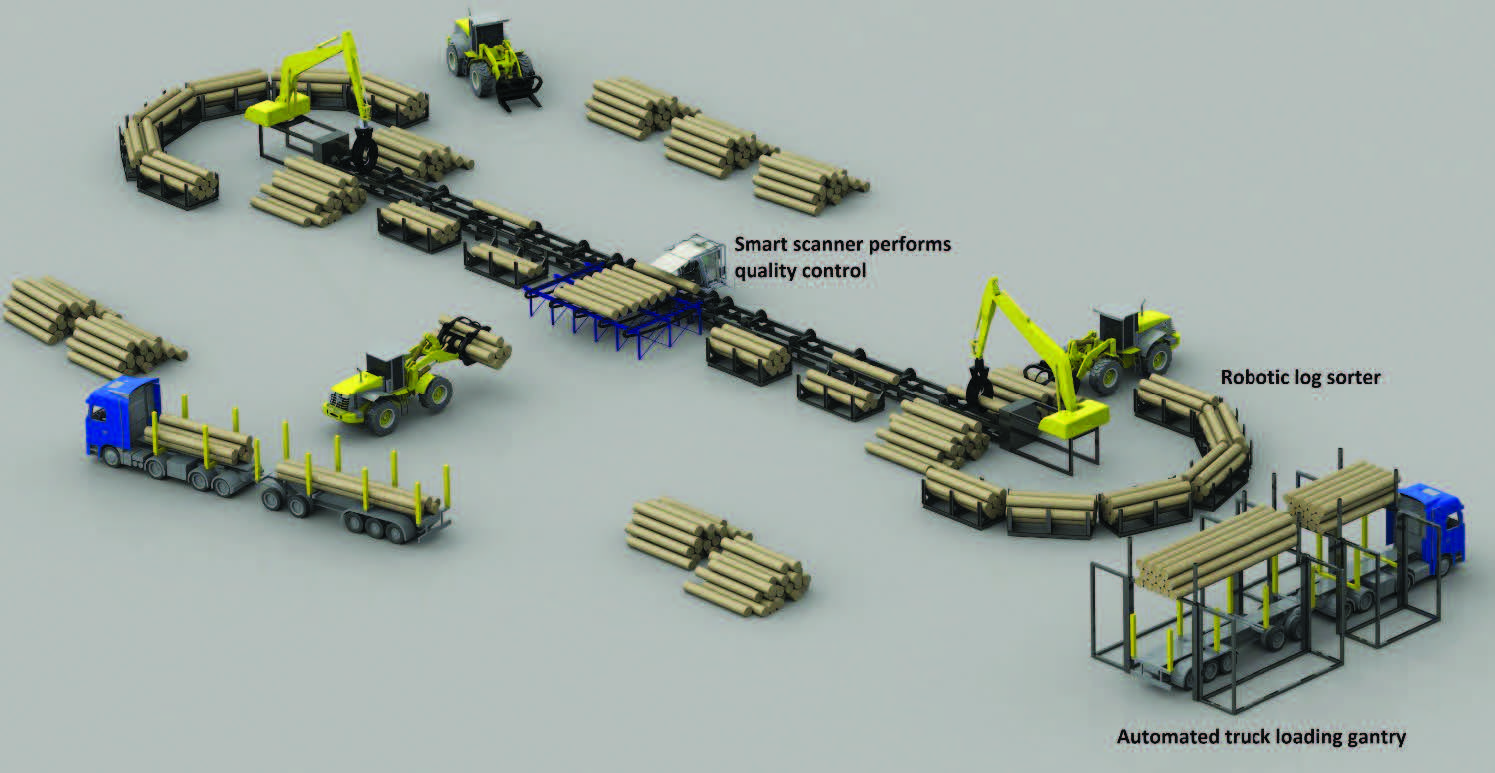
The sort yard opens up more opportunities for large volume high productivity motor vehicles which are often too big to get round tight forest roads. However, their ability to carry more logs than a traditional log truck on the highway improves productivity.
The potential is for each of these log sorting facilities to be able to service a number of harvesting crews or a number of small forests whose owners can get together and coordinate their harvest to maximise the opportunity. Up to 2,000 cubic metres of logs are envisaged being handled each day. Individual log identity ensures each owner’s wood is identified and kept separate for invoicing and payments.
Significant benefits
If the programme is successful, as much as 95 per cent of all harvesting and logistics operations will be fully mechanised and at least 10 per cent of all harvesting operations will be automated. That would lead to significant benefits across the board, with targets being −
- A reduction across the forestry value chain of $10 a cubic metre of wood, making small forests more economic to harvest
- Improving the attractiveness of forestry as a career for skilled workers, along with improving safety.
- Alleviating the need for the estimated 800 additional workers in the industry with increased productivity and more automation
- Reducing log landing construction areas by up to 75 per cent
- Reducing the amount of chemical fumigant for export logs by 10 per cent with debarking in the forest
- Producing innovative new equipment and systems which could earn New Zealand manufacturers more than $50 million in sales by 2025 – Forest Growers Research estimates as many as eight or nine new types of equipment could be developed.
Working with forest owners
Forest Growers Research is looking to work with a number of forest owners, large and small, as well as their contractors, to set up five sort yards which could be serviced by up to eight crews per sort yard. That would be 40 hauler crews who would supply those five sort yards. In addition, 12 automated ground-based crews are planned. From that size of operation, profitability to the forest grower can be improved in a number of ways. First, labour productivity of hauler crews will be increased by making them a lot smaller. Potentially, a large crew of nine or ten workers could actually be split into two crews of four or five, each producing the same volume of wood as the larger single crew currently does. This reduces harvesting costs and improves profitability.
More efficiencies can be introduced including semi-automated log processing, automated sorting and tele-operated or automated log loading. By improving log measuring and individual log identification, logs can be sold by volume rather than weight, taking out costly operations such as weighbridges and manual log scaling at the port which cause a lot of truck delays.
It does not stop at the economic benefits. Sustainability benefits include improving or maintaining the social licence to operate, so that the community actually sees that harvesting and log transport is a good safe business, and one which is looking after its people. In terms of environmental sustainability, in addition to reducedsoil disturbance with smaller log landings, another area which has major environmental potential is in reducing chemical fumigation of export logs. A lot of money is spent fumigating logs for export, and this cost is forecast to double after 2020, when complete recapture of methyl bromide becomes a requirement. If we can successfully debark logs on the landing to the standard required by Chinese log customers we may not need to fumigate as many logs.
Reducing environmental footprint
There is further potential in collectively managing log making residues which are currently unmerchantable, so they produce revenue instead of being a disposal cost. More use can be made of the high productivity motor vehicles which can carry more logs than standard logging trucks from the sort yards. If we can implement 58 or 60 tonne routes from the five in-forest log sort yards, this would result in over 9,000 fewer truck trips a year on the public highway by 2025.
The value to the forest industry of improved environmental results is estimated to be over $10 million a year by 2025. More importantly, we need to continue to reduce the environmental footprint of forestry operations. If you fast forward five or 10 years into the future we will not be able to cut large landings into hillsides, produce lots of tracking and leave piles of log residues around landings.
Concern regarding economic viability of small-scale steep country forests, and future environmental and social sustainability is driving these developments. Forest Growers Research is keen to see small-scale forest growers participate in the new programme.
If your forest is coming up for harvest we encourage you to ask your harvesting and marketing company, or your harvesting contractor, what innovations they are developing to reduce landing size and roading infrastructure, improve environmental results, and increase value recovery from your crop, to improve your forest’s profitability. This will ensure that your future harvest is viable both economically and environmentally.
Keith Raymond is Harvesting and Logistics manager at Forest Growers Research.
