Harvesting a small woodlot: Trials, tribulations and lessons
Gavin Adlam, New Zealand Tree Grower November 2016.
In 2015 we engaged a contractor to harvest our small block of pines – approximately 2.5 hectares – on our six hectare block. The trees were planted in about 1994 and 1996 before we bought the block in 2003. Our vision was for this to be carried out over a short period and with a minimum of disruption to our lives and property. The hope was to earn enough money to pay for restoring fences and for cultivating or planting the harvested area.
In fact, the project fell short of our expectations in several respects, although we eventually managed to get a reasonable result. This is a brief account of our experiences and some of the lessons which can be taken from them.
The older crop had been pruned and thinned in about 2001. Apart from that, we knew very little. With some guidance from Hamish Levack, and in making our own plans for the land, we decided to remove some of the trees to make way for orchard and amenity plantings. We retained the rest of the trees and arranged for them to be thinned and pruned, with the idea that we would keep our options open. We also joined the Wellington Branch of the NZFFA with a view to learning more about pine trees and how they could be dealt with.
As we learned more, and as the pine trees grew, we came to realise that there were some constraints on our options for harvesting. Some of those constraints were self-imposed – we were developing our property with pasture, livestock, fences and other plantings. We did not want it compromised by logging operations.
Access to our property is constrained for the last kilometre by a one-lane bridge with a 20 tonne weight limit followed by 500 metres of gravelled, shared driveway. From the driveway to the skid sites was about 200 metres over a low ridge and across our best hay paddock.
The trees themselves were reasonably accessible for harvesting. About a quarter was growing on flat areas, suitable for skid sites. Another quarter was growing on easy ground adjacent to the skid sites and about half was on the banks of a steepish gully, interspersed with native remnants and other regrowth.
Background research
We thought about various ways of dealing with the trees. We visited several other sites on Wellington Branch field days, and we hosted a Wellington Branch visit, to show what we had and to pick the brains of experienced NZFFA members for ideas about how to deal with our crop. Several particular points came out of all this, including −
- The amount and quality of the crop was good enough to justify seeking a buyer
- We did not want a gravelled logging road built across our flat pasture, but it was adequate for trucks to drive over during dry weather;
- The weight limit on the bridge would be a severe and costly limitation, unless some way could be found to aggregate the logs on the other side into full truck and trailer loads.
One of the turning points was a Wellington Branch field trip in September 2014, hosted by Peter van Gosliga, demonstrating his techniques for harvesting a small woodlot. Peter’s system was to use a large tracked excavator with a grapple and other log handling machinery, including an onsite de-limber, and to coordinate the sale of timber by a variety of channels including local sawmills, export and firewood
We were still reflecting on this a few months later when we discovered that the pine trees on a neighbour’s property were being felled and harvested using a similar system. We spoke to the operator, who explained that he had secured the use of some land immediately across our weight-limited bridge. This meant that logs could be carried across the bridge in permissible single truck loads, then sorted and aggregated on the other side for consignment of truck and trailer loads to the final destinations. After site visits and further discussions, the operator expressed a keen interest in harvesting our logs immediately he finished at the neighbour’s property.
Managing the problems
We could see that there were some uncertainties and risks which we hoped to avoid or manage. As it happened, most of those risks became a reality and they turned out to be more difficult to manage than we had envisaged. Some old lessons were reinforced, and there were some new lessons for us.
We were assured that the whole job should take no more than a couple of months. This seemed reasonable as the ground was already dry and we were expecting a dry summer. However, we insisted on a sequence of harvesting which allowed for the creation of skid sites, followed by harvesting the trees from the steep gully area before the remaining less difficult area was harvested. In addition, we incorporated the remains of an old shelterbelt on the boundary with a neighbour at the top of our section. The trees – about 40 in total could be extracted through the neighbour’s property with close access to the gravel road. If work had to be suspended or terminated for weather or any other reason, we wanted to ensure that the trees still standing were the easiest for us to deal with later.
As each area was harvested it would be tidied, the slash either pushed over the bank where it could be left to rot or on the flat, stacked in burn piles to dry. Slash would be removed from the creeks. We got agreement from the contractor on what fences we would have to dismantle, and when. Fence lines would be left graded reasonably level and clear of logs or slash, so that we could reinstate the fences.
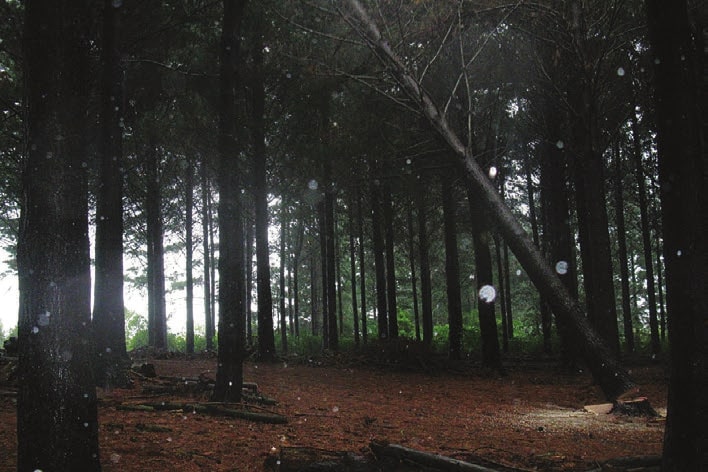
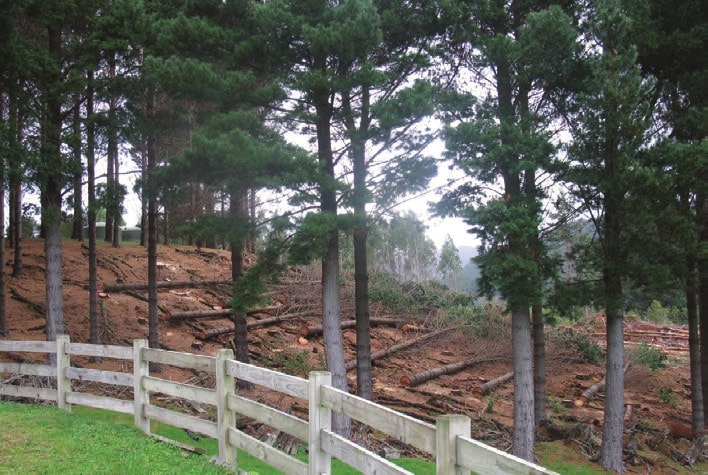
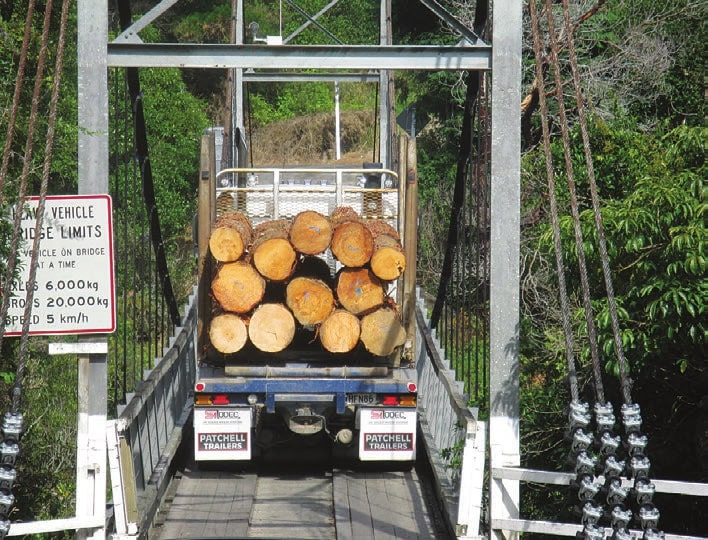
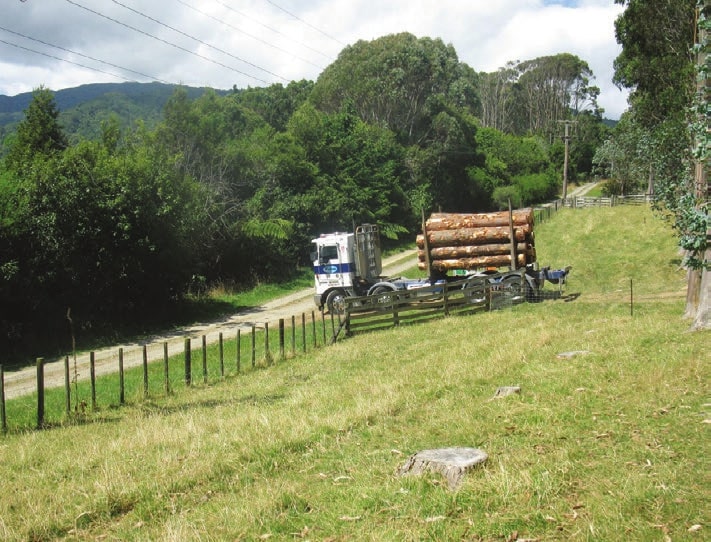
Discussions with contractors
The contractor offered a price of a few dollars per tonne of logs as removed from the property. The amount was not large, but definitely worth having and enough to cover the costs we expected to incur in reinstating fences and pasture and in planting the harvested areas. It was also enough to justify proper record keeping.
The operator explained that the work would be undertaken by a company for which he was, in effect, the operations manager, and he put us in touch with the managing director to discuss contract terms. In speaking to the managing director, I got confirmation of the company name and he promised to forward to us a form of contract.
We had a couple of follow-up visits during January 2015 which was fine and dry and would have been wonderful weather for harvesting. Although we had several contacts during that month, the start date was always about a week or so away. This was an indication that the contractor might have problems keeping to timetables.
Preparing the contract
I did make some progress on preparing a contract – which highlighted for us some additional risks. I searched the company details on the public register and discovered that it had been formed only a few months previously. It meant that this was a new business, without a track record and no indication of how long it might continue in business.
The draft contract which the managing director sent to me was a template for harvesting, but did not provide for the sale of logs. Therefore, it seemed that the contractor was not very diligent about recording the proposed contract terms. Fortunately, that was a task in which I could claim some experience, and I was able to submit a fairly simple contract which, I believed, reflected all the matters which we had been discussing.
It is an old lesson, which served us well in this case, which is to insist on some form of written contract, and be involved in the preparation of it. The contractor’s template may not be suitable, without amendment. In my view, the contract should at least serve as an operating manual for the project – set out the expectations which each side has of the other, the timelines and steps to be taken if things do not go as planned.
The process of discussing what should be in the contract is often an extremely valuable aid to everyone in clarifying their expectations of each other. In addition, where there are several people with an interest in the trees – such as in a family block, a trust, a company or partnership – the process of getting their agreement to the contract can be invaluable. It should ensure that their preferences are included and that if things do not go as expected, there is less likelihood of an internal dispute.
One area of risk which concerned the contractor and ourselves was health and safety. We pointed out that we had no expertise in the proposed operations and expected them to take responsibility for health and safety on the site. We identified any hazards which we knew of. They provided hi-vis vests to use if we wished to go on site, and emphasised the need to see and be seen. They also explained that the workforce had to be qualified for various tasks. This was all done by word of mouth – we did not insist on seeing any paperwork and they did not explicitly offer it.
Counting the loads
In our case, as we had no means of measuring the weight of logs taken, we agreed that the dockets for onward cartage would provide a record and be used as a basis for invoicing. The contractor would provide a buyer generated invoice for GST purposes.
In fact, the contractor’s record keeping was reasonable for the first two months, but after that degenerated to the point where it was impossible to reconcile the logs taken with the payments. As it happened, principally out of curiosity and a certain obsession with counting things, we counted the loads taken off the property. This turned out to be very useful to us in the latter stages as it prevented the contractor disputing the quantities taken. The result may not have been more money for us, but it certainly reduced the likelihood of a messy and possibly expensive dispute.
The harvesting begins
The contractor’s equipment came on site in late January, and at the beginning of February it rained. The crew consisted of the digger operator who was also the site manager along with one or two chainsaw operators and occasionally, a specialist tree feller.
From the outset the project did not go as quickly as we had hoped. The two months extended into a fifth month and eventually we agreed to terminate the project in late June. In the early period time was lost due to a series of machinery breakdowns and various reasons for personnel being off site. As the months passed, shorter days and more rain meant more time lost waiting for better weather and from dealing with broken-down or bogged vehicles. A considerable part of our pasture was churned into mud, and they managed to roll three or four logs through a fence around our native plantings, despite earlier discussions and our contract.
The contractor had an arrangement with a transport company to collect the logs from the skid site with a single truck and take them over the river to the temporary storage. From there, the same driver was able to take a fully laden truck and trailer to the destinations agreed with the ultimate purchaser – the port in Wellington or one of the local sawmills.
The first truckloads went out on 20 February, but there seemed to be difficulties in scheduling the trucks and by early April arrangements with the transport operator had apparently been terminated. Various ad hoc arrangements were made for transporting the logs to the assembly site across the river, all of which were erratic and time-consuming.
The contractor was highly incentivised to clear all stockpiles before the end of each month in order to get them delivered to their final destination and get paid. Because of the amount of lost time, this inevitably meant a big rush to extract logs whenever possible, and less attention was paid to cleaning up.
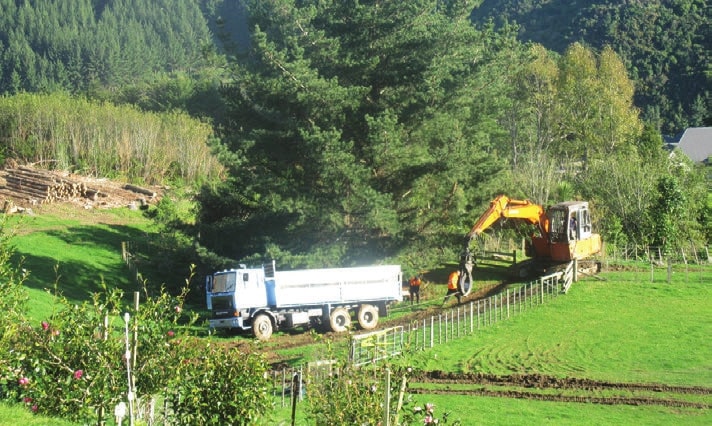
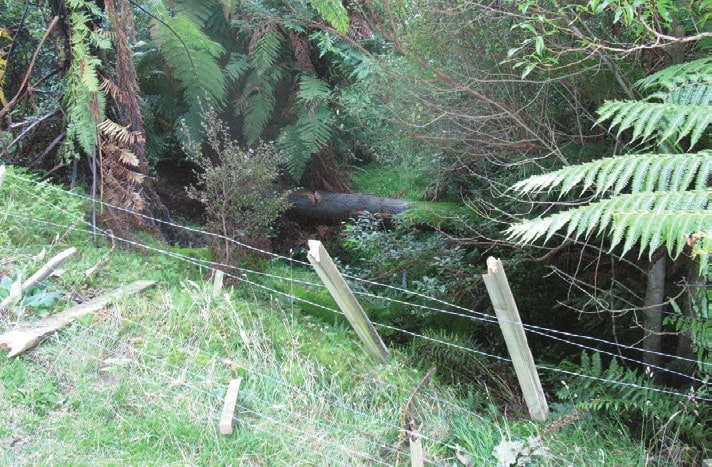
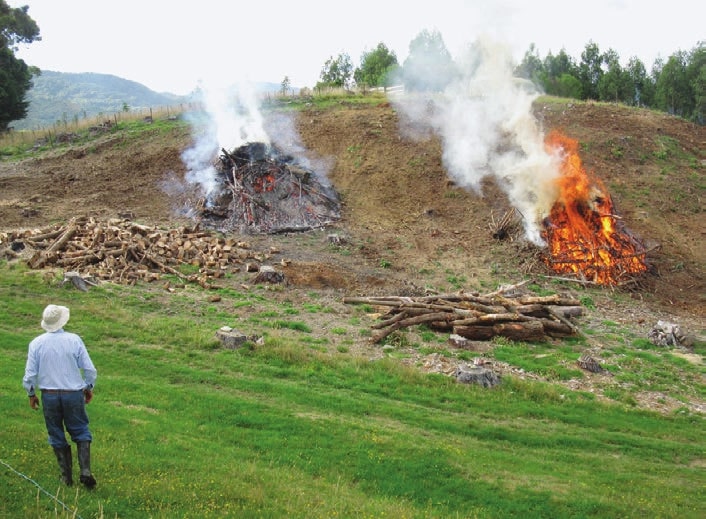
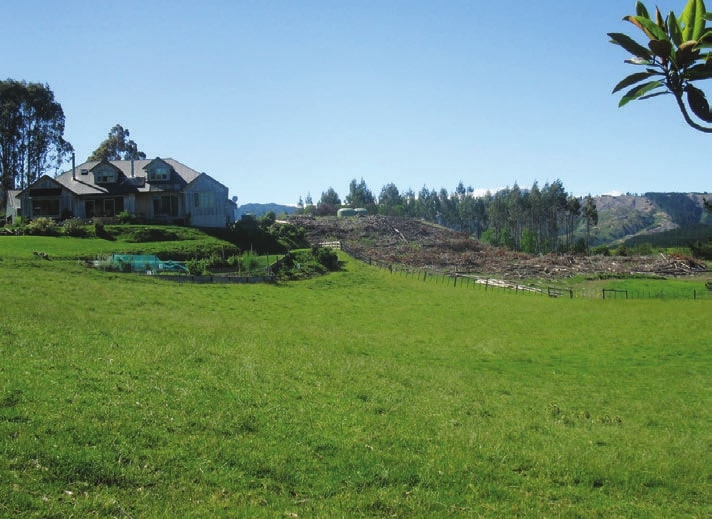
The end in sight
By early June the contractors had taken out the most valuable logs from the original skid sites and established a metalled skid site on the neighbour’s property to take out the remaining logs through that route. This entailed a lot more travel with the digger over the already wet ground, pulling logs up to the access point and taking the slash down the hill clear of the skid site.
By the end of June it was evident that the crew had really done all that could be done. They had felled all the trees, taken the most valuable logs, made a much more comprehensive slash mess than we had contemplated, and they were a long way from completing the sort of tidy-up that we had asked for, and which they had agreed to. In addition, the payments for April and May due in May and June fell short of what we had expected. When I discussed this with the managing director, the fundamental message was that the company had not been operating as profitably as he had planned and he did not expect to be able to pay the full amount.
He undertook some tidying up around our right of way and the neighbour’s property, and we agreed that we would call it quits. As a result, we were left with most of our original plantation area covered in slash, mixed with logs. Some of these were already stacked in piles and many limbed and ready to extract, but very few big enough to have much value in the log trade.
The contractors left at the end of June. We had a wasteland of slash, much of it mixed with large branches, mud and small logs, completely unmanageable with our resources, and with rather less money in the bank than we planned. By that time, we were grateful to see them off our property.
The solution we found, which in the end was much more satisfying, was to engage a willing firewood merchant with a moderate sized digger. Over the course of the summer, he worked his way through the piles of firewood and slash, took as much of the firewood as he wished and stacked the slash into a series of burn piles – at one stage there were 14 ready for our attention.
Although the job is still not quite finished, we spent the summer tending fires, replacing fences and restoring the property to where we expected to be in autumn 12 months earlier. We were finally able to plant grass in the 2016 autumn over most of the harvested area.
