Increase profitability of harvesting - small-scale forests on steep terrain
Keith Raymond, New Zealand Tree Grower November 2012.
There are many challenges facing the forest industry due to decisions taken in the past. In the 1980s and 1990s the plantation forests in New Zealand increased significantly. Many areas of marginal pastoral land throughout the country were planted in pine trees, often in places where sheep and goats had difficulty staying upright and distant from towns, cities, sawmills and ports.
An additional 300,000 hectares were planted over a seven-year period from 1992 to 1998. Many of these forests were established by forestry syndicates, partnerships and land owners of small areas. These occupy almost 40 per cent of the national forests and include around 15,000 owners. They have a wide geographical spread, a broad range of forest sizes and ages which in general fall into the post-1989 forest age groups.
Some of these small-scale forests owners are harvesting their forests now. However, the large-scale owners, who have over 70 per cent of the pre-1990 forest, will continue to dominate harvesting volumes until around 2015. Large areas of the forests owned by small-scale forest owners will become ready to harvest from about 2016 onwards. From that point on, wood supply from small-scale forest owners will start to dominate the harvesting scene.
Planning and roading challenges
Over half of the national forest is first rotation forest. That means the forests that have not been logged before and probably have few logging roads, apart from the original planting tracks. Of the identified first rotation forests, 64 per cent are aged over 16 years and available for harvest within the next 10 years. Deducting the area of the next two years’ harvest, which is probably already roaded and harvest ready, the forest due to be harvested in the next 10 years of approximately 500,000 hectares is not roaded.
Plantation ownership
Forest type | Years till harvest ready | Age class | Owners of forests over 10,000 hectares | Owners of forests under 10,000 hectares | Total |
---|---|---|---|---|---|
Post-1989 | More than 15 years | 1 to10 | 322,402 | 157,284 | 479,686 |
11 to 15 years | 11 to 15 | 220,515 | 215,559 | 436,074 | |
6 to 10 years | 16-20 | 137,192 | 200,518 | 337,710 | |
Pre-1990 | Less than 5 years | 21 to 25 | 182,232 | 48,532 | 230,764 |
Now | Over 26 | 189,672 | 63,685 | 253,357 | |
Total | 1,052,013 | 685,578 | 1,737,591 |
This situation is exacerbated by the relative isolation of the forests, steep terrain and small forest size meaning there is a lower harvest volume to offset against roading expenditure. Significant expenditure is required to build roads for harvest access in these forests, and it is doubtful that there are enough skilled harvest planning and engineering resources for this task.
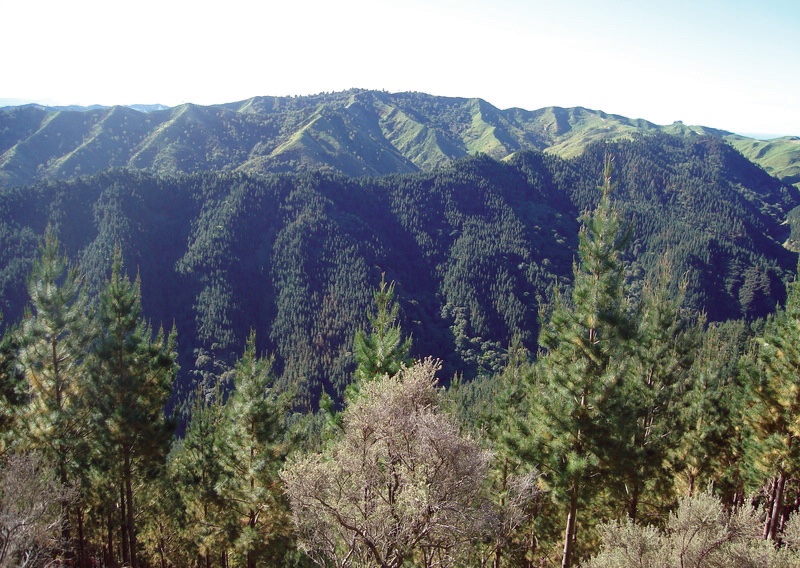
Harvesting challenges
The steep land and fragile soils and our environmental constraints mean that harvesting by cable haulers is frequently the only option. This cost may be up to double that of the more cost-effective mechanised ground-based systems. Over the last 35 years cable logging has tripled from 15 per cent of harvested volume to currently 45 per cent.
The expected annual increase in the proportion of cable logging will push average harvesting costs up by almost one per cent a year, with no change to logging rates. Cable logging costs will therefore have to be reduced just to maintain current average harvesting cost. The average cable logging crew has nine workers with four machines cutting 216 tonnes a day for about a $32.80 a tonne logging rate.
Cable logging methods have not changed much in the last 35 years. The most common rigging systems are those which have been around since the early part of the 20th century. The last major innovation in cable logging in New Zealand was the introduction in 1987 of the swing yarder, which can operate on small log landings, and the widespread conversion to knuckle boom loaders in the early 1990s.
Log processing and value recovery
The intensive pruning and early thinning management practised over the last 30 years in many of these forests means that the final tree crop is now large, at 2.5 to 4.0 tonnes a tree, and heavily branched above the pruned log. These trees are not conducive to efficient mechanised harvesting systems. Tree felling is still mostly by chainsaw and processing in over half of harvesting operations is still manual.
From the early days of log grade segregation into mainly pulp and saw logs with one or two long length export grades, there has been an increase of log grade complexity. The average number of log grades sorted in the forest is now 10. This presents a challenge in terms of log value recovery, processing productivity and cost, landing space and loader operator workload. From a traditional wood product point of view, high production costs are caused by steep terrain, challenges to mechanisation and long transport hauls to market. Profitability is therefore lower.
Solutions to low profitability
The economics of forestry are affected by a large number of factors. Delaying the harvest would only make the harvesting operation more problematic, and deciding not to harvest at all could have a serious effect on the sustainability of the harvesting workforce. Extending the harvest age beyond where tree size is manageable by current mechanised harvesting equipment would result in a return to manual harvesting methods with labour and safety problems. The only realistic solution is a major increase in the profitability of traditional forestry and wood products.
Little can be done about the quality of the forests maturing quietly on those marginal hillsides, or about the domestic or export log prices that are too low. We can add to those the increase in fuel costs and the probable fall in the exchange rate back to historic levels.
Reducing costs
What can be affected and controlled by the forest owner? The profitability of forestry can be improved significantly by reducing the cost of harvesting as this process uses up to 40 per cent of the average delivered price of a log. The good news is that cable yarding is a commonly used and well-known harvesting method in New Zealand. With almost half of the harvesting currently being done by cable logging systems there is a core of entrepreneurial contracting firms in this sector.
How to reduce cable harvesting costs is a $90 million dollar question. It has been estimated that innovations in steep terrain harvesting could reduce cable logging costs by a quarter of the average cost of $32 a tonne. The current annual harvest is 26 million cubic metres, of which almost half is from steep terrain, so this will benefit the forest industry by over $90 million.
There is no silver bullet, but achieving these savings is ‘no worker on the slope, no hand on the chainsaw’. A research and development programme, based around a primary growth partnership, is being aimed at improving productivity. The target is to reduce harvesting costs by at least 25 per cent and make harvesting jobs safer and more desirable for workers.
Forest planning
The small-scale forest owner can help by using economies of scale. One example is in planning the harvest areas to be as large as possible. A limitation on volume production may be the size of the contract area and the time lost in moving the location of operations. In 2011, the average harvest area size was 16.9 hectares and ranged from 4.4 to 48 hectares.
If the small-scale forest owner can increase the size of the harvest area by forming cooperatives or amalgamating stands at time of harvest, this will have a positive effect on harvesting productivity. The graph shows the relationship between productivity and harvest area size.
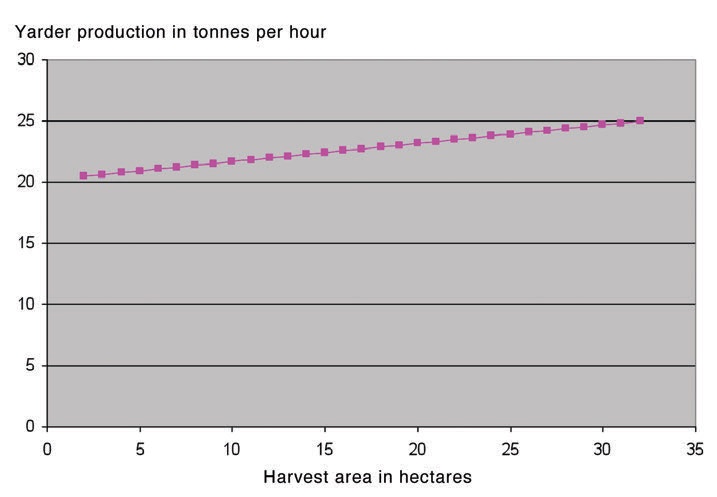
An increase from 15 hectares to 30 hectares enables an increase in harvesting productivity of 10 per cent by reducing lost time and with lower handling costs. Other factors being equal, for each five hectare increase in harvest area size, daily production will increase by about six cubic metres. It is more economical to keep the harvest areas as large as possible to for the maximum production harvesting crew to work than to try and put a large crew into a small harvest area.
Harvest planning
Harvest planning is carried out so that the right harvest system is used, and is one which achieves the silvicultural and resource management objectives of the forest owner. The harvest system selected must be efficient and feasible. It must also be socially acceptable, with safe operating practices, and meet all forestry regulations and best management practices.
In steep country the economic and environmental success of skyline harvesting is influenced by the type selected and by how well it is positioned on the land. Good planning is needed to develop well-positioned skyline spans. Proper positioning of these spans enables hauling an optimal volume of logs in each cycle, which results in the best solution for production, rope wear, suspension and soil disturbance.
Payload is constrained by the maximum load or tension in the cable and the available sag, known as deflection. Deflection is the vertical distance between the chord slope and the skyline, measured at mid-span and expressed as a percentage of the span. The more deflection, the less tension in the cable, and the more payload can be hauled.
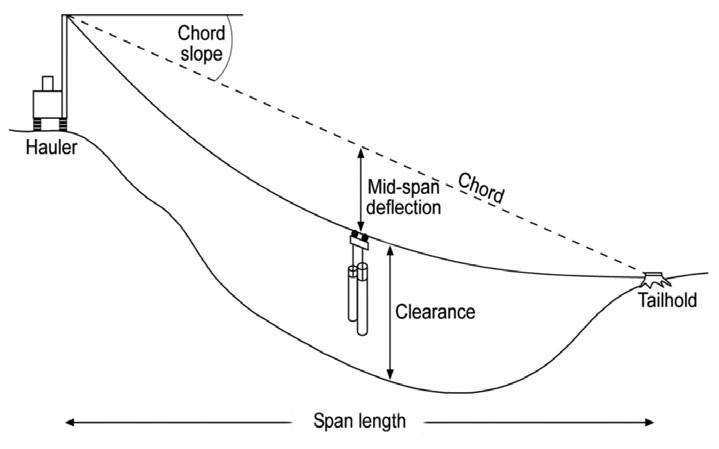
Poor positioning of the skyline spans can result in little suspension, excessive soil disturbance, hang-ups on obstacles, reduced production, rope failure, equipment breakdowns, unsafe operations and unworkable harvest areas where tree stems cannot be extracted. To maintain a consistent volume, and provide a balance between harvesting production and road construction, an analytical planning process is required where a range of alternatives is considered.
One recent innovation is the development of cable hauler planning system. This integrates a computer software planning package with a geographic information system. Using this, harvest planners can sketch a network of skyline harvest settings directly on to the topographic map in the geographic information system − proposed roads, landings and hauler setting boundaries. It can also calculate payloads for proposed hauler spans. Then the harvest planner can analyse total catchment area harvest plans for the small-scale forest owner rather than doing plans by approximation.
Roading and landing construction
The landing size required will increase by almost 700 square metres for every four log sorts added to the cut plan. At average production of 200 tonnes a day, a crew with a cut plan of seven log sorts needs a planned landing size of 2,300 square metres. The same crew with a cut plan of 11 log sorts requires a landing of 3,000 square metres, and if the cut plan is expanded to 15 log sorts the landing size must be 3,700 square metres.
This equates to an increase in landing density of one to two per cent of forest area for every four additional log sorts, depending on landing spacing. This loss of forest production is a major consideration, particularly for the small-scale forest owner.
In large-scale forestry where stumpage sales are the exception rather than the rule, roads are considered as an asset to the forest. The underlying principle has been that it is better to undertake a good standard of roading to keep harvesting crews working due to the high daily cost, and keep the trucks rolling, than it is to move.
Reducing roading costs
With the trend to small forest ownership, and where forest lands change ownership at the conclusion of current rotations, expenditure on harvest access is a sunk cost. This is unless the landowner requires a permanent road for access to other parts of the land.
Where roading costs are much higher than the New Zealand average, such as the East Coast, and with increasing environmental pressure, one alternative is to keep the investment in roads as low as possible and move the logging crews when conditions worsen. In other words, build roads to as low a standard as possible to extract the wood.
When it rains and the water table rises, skid trails start rutting and haul roads start to collapse, so you move the harvesting crew to another harvest block. This method is used on the east coast of the United States by swamp loggers as timber in these areas is commonly purchased on a lump sum stumpage basis and any expenditure on roading is a sunk cost. As a result there is a tendency to avoid large expenditures on roading.
Tree felling
While the aim of tree felling is self-evident, it is useful to reflect that the main aim of good practice in this area is to help with the extraction phase. That means felling the tree in such a direction that the following operations of de-limbing and extraction are as efficient as possible. A pre-requisite is that the work is performed in a safe way. Many studies have indicated that with manual tree-felling, considerable value is being lost. In the past, much emphasis has been placed on trying to improve manual tree felling practice for satisfactory conversion into the log grades.
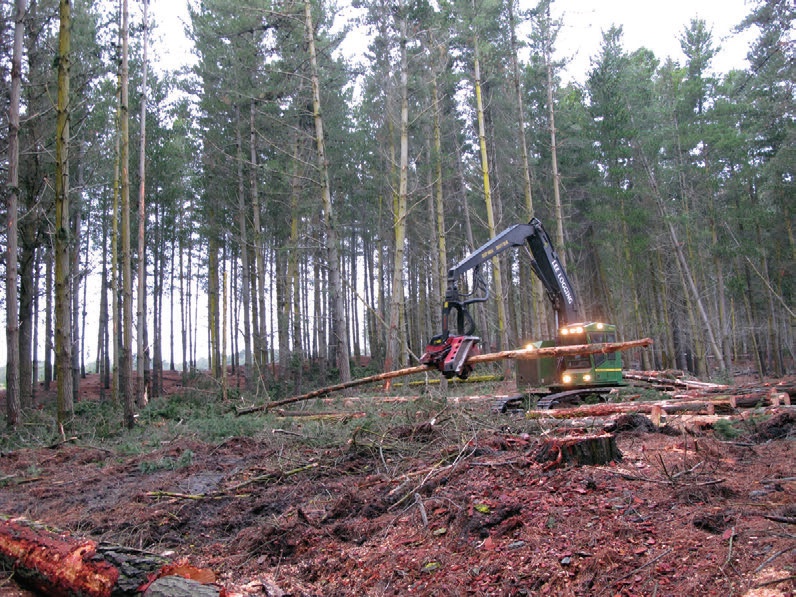
It is well known and understood that large radiata pine trees break during felling, often at relatively short tree lengths. The volume of the broken stem is therefore low relative to its diameter, and this reduces the potential value from these broken stems. There is a shortage of skilled workers in the forest industry and high physical workload associated with good manual tree felling practice. Therefore it is uncommon to have harvesting practices which maximise value recovery, such as low stump heights and cross-slope felling.
The safety and productivity benefits of mechanical felling are well known and often quoted, but the value recovery benefits of mechanised felling are often overlooked. Reduction in stump height by mechanised felling is a significant saving. In the average radiata pine clearfell block, a 10 centimetre reduction in stump height will recover about six cubic metres a hectare of pruned log volume worth $700 a hectare. Mechanised felling is the only practical way to consistently perform cross-slope felling and gain a reduction in tree breakage during felling.
New machines and systems are being developed to mechanise the felling and pre-bunching on the slopes with the aim of eliminating manual chainsaw felling in cable operations. Successful operations are using excavator-type loaders bunching on slopes.
Cable extraction
One innovation for grapple yarding is a new restraint which has been developed by Future Forest Research to improve grapple control. This solution to the uncontrolled movement of rope grapples has had extensive testing in the field and has now been released to logging contractors. It was found that the time saved was only three to four seconds per cycle, but this resulted in payback on the grapple restraint in less than two months.
A 2011 benchmarking survey indicated very few cable operations use two-stage operations. Two-staging involves an extra machine, such as a skidder or a forwarder, to extract from the primary extraction machine to the processing area. Although this is an extra cost to the contractor it provides the opportunity to reduce roading costs.
The average two-stage distance is around 230 metres, which at a roading cost of $50,000 a kilometre, is worth $11,500 or about $1.40 a tonne over the average setting volume of 8,200 tonnes. When all other factors are taken into consideration, two-staging is generally more productive, eliminating interference delays between functions, and it results in a lower average harvesting and roading costs over single stage extraction.
Conclusion
So what does the future of cable harvesting look like and what will it change into? Mechanical felling and bunching, using the Trinder ClimbMax and grapple yarding using the Alpine or Falcon radio controlled hydraulic grapple carriage, is the solution for difficult terrain. The ability to mechanically fell and bunch safely on all steep slopes opens up the opportunity to de-limb on these areas, to reduce stem weight, and enable extraction with smaller faster cable yarders.
Imagine a system where there are no landings, where innovative low-ground pressure high speed cable yarders walk down ridge lines and perch out as far as necessary to access all the wood in a setting without having to build a road to the landing. Bunched wood would be extracted by grapple to the nearest ridge line and then two-staged to a separate processing area using all-terrain forwarders and loaded directly to a truck.
No hand will touch the wood and no worker will be on the slope. This would put steep terrain harvesting on a pathway to growth, with reduced costs, enabling increased harvest levels and eliminating lost time accidents in felling, breaking out and extraction operations. New investments in machinery and new employment opportunities in safer, higher skilled jobs will result.
The government will continue to make new investments in harvesting research and development to support small- scale forest growers to improve the profitability of forestry. Improvements can be made with a concerted effort from forest owners, loggers and engineers in steep terrain harvesting. Small-scale forest owners who are not already involved in the harvesting development programme are encouraged to become a stakeholder in harvesting research.
Keith Raymond is the theme leader, for harvesting and logistics, Future Forests Research Ltd
