Milling and grading New Zealand grown blackwood
Mike Esson, New Zealand Tree Grower August 2006.
Blackwood is a much sought after timber, especially by cabinet makers because of it rich dark colour and fine finish. Blackwood is a species that brings people to our yard because of its dark colouring.
Our customer base is growing in number and variety, from cabinet makers and joinery firms through to very specialist woodworkers making and restoring gunstocks or musical instruments, and all manner of other interesting things. We also supply people building their own houses who want something different for the ceilings and floors.
Sources of blackwood
The nature of our business means we are milling a lot of one-offs. These are often large individual trees or occasionally small groups of the same species. Some of the trees come from farms, some from urban parks, roadsides, riverbanks and gardens.
If individual owners ask us to mill a tree for them, our system is to mill the tree in return for half the timber. After all, we want the timber and not just to operate as contract millers. The remaining half of the timber belongs to the supplier, who can then sell it back to us, use it himself or sell it to someone else. We are also increasingly selling the owner’s share on their behalf, which includes seasoning, grading and marketing.
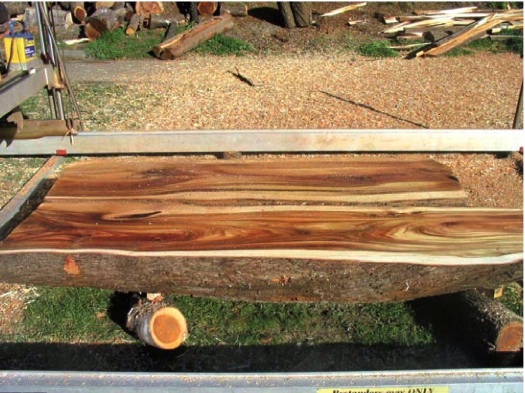
Tree owners’ expectations are generally high, but wood recovery can be very low, especially from small logs. The average saleable grade recovery from the blackwood we mill is only around 20%. The maximum recovery we have ever achieved is 23%. Even with a log that looks good you do not know what you are going to get until you mill it.
Milling the logs
Generally the trees we mill have never been managed for timber production. The logs tend to be rough, difficult and time-consuming to mill. We run a Pedersen sawmill and mill to grade. That is we mill boards that we are likely to sell. This tends to be higher grade boards. We avoid the sap and mill around defects, aiming for lengths that are as long and clear as possible.
To achieve this we often drop down to 50 mm board widths. The maximum board width achievable is 150 mm. It becomes nearly impossible to cut anything wider of any useful length without including rough defects. The market is virtually zero for knotty boards or those with sap on three faces.
The most commonly requested longer lengths are two metres to 2.4 metres. These also happen to be very difficult to mill from untended trees and as a result we tend to build up a steady surplus of shorter lengths. We have adapted our method of grading and sales to ensure we sell shorter lengths along with the requested longer lengths. We cannot afford not to sell short lengths. In effect we ration the longer lengths, supplying specified lengths to match a customers cutting list. We also endeavour to provide timber from the same log or group of trees to ensure a colour match. Colour can vary noticeably from one tree to another, and trees from one location to another, as can timber density.
Drying and grading
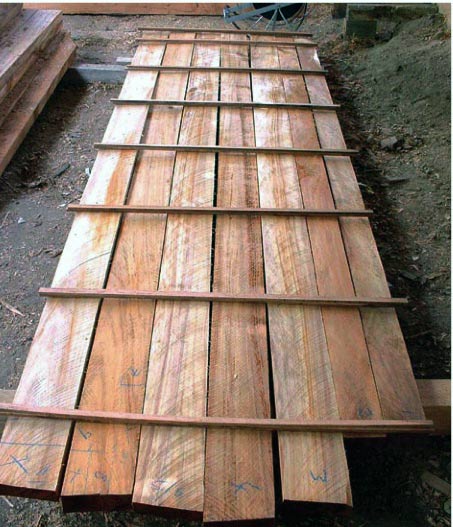
Timber milled from other people’s logs is taken to our yard, graded, filleted and placed under cover as soon as possible. The grading determines the value of the log supplier’s share. Timber milled from our own logs is graded across a docking saw to remove the worst defects, then filleted and placed under cover. We then specifically grade it for sale and entry into our inventory once air dry.
Many of the species we mill incur further defects during drying. Often the timber graded off the saw requires re-grading once air dry. Blackwood can vary markedly in drying defects. The less timber defects, the lower the drying distortion. Crook and bow may show immediately after milling or close to air dry. Air drying the timber can take between six and eighteen months depending on timber density and time of year it was milled.
When an order is confirmed we undertake further drying in one of our dehumidifier kilns, taking it down to between 10% and 12% for general interior use. The time taken to kiln dry the timber can vary from seven days to many weeks, and depends on the timber dimensions and density. We can lose further timber in the kiln drying process from distortion and shrinkage, but have learned to minimise this by taking our time. Blackwood can be kiln dried from green, but again the results vary, sometimes with minimal drying defects, other times with as much as a 20% grade loss.
I suspect that tended trees will be less variable, as they are likely to have straighter grain, lower trunk tension and less internal defects. It is hard to make specific judgements on the properties of a species such as blackwood when the resource is so variable.
Big is good
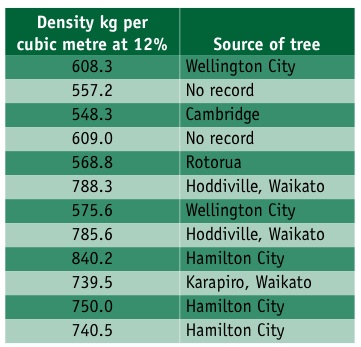
Bigger, older trees tend to produce better wood. My preference is for butt logs of over 80 centimetres diameter at breast height. My experience with trees in general suggests that the larger the trunk diameter, the lower the wood stress from supporting the upper tree and canopy.
Blackwood colour can vary noticeably. All colours sell equally well, although this may be related to limited availability because the richer brown is generally preferred over the duller grey. Cabinet makers making commissioned one-off furniture definitely prefer timber that will colour match. We do our best to supply these customers with timber from the same tree or group of trees, reinforcing the advantage of having a bigger tree to start with. Larger users making laminated products like bench tops may mix and match to provide an overall balanced pattern or colouring.
Markets and price
Generally we are cutting for furniture and bench tops, and the demand is for straight, clear timber. The market for low grade boards is very limited. We retail the timber at $3,000 a cubic metre. Widths greater than 200 mm attract a premium of 10% and lengths over two metres attract a further 10% premium.
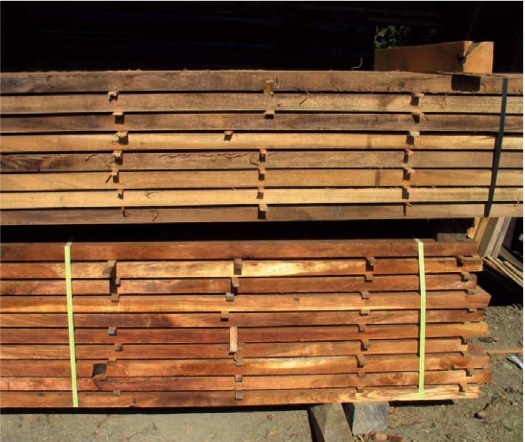
Overall, blackwood is expensive to mill and grade – much more so than comparable species such as black walnut, so we need a good return to make anything out of the process. This means it is relatively expensive to make furniture out of blackwood. The timber can be difficult to work, but it does finish very nicely.
I think blackwood is a species with great potential. The demand is strong and increasing, and the more people get to know of it, the greater the demand is likely to become. We are always interested in acquiring blackwood.
Mike Esson is joint owner of Rarefind Timbers with business partner John Woolford.
